Glass candle jars are popular for their aesthetic appeal and functionality. Ensuring their quality is critical for safety, durability, and customer satisfaction. Below is a comprehensive guide to inspecting glass candle jars, covering key inspection points, procedures, and precautions.
1. Key Inspection Points
1.1 Visual Quality
- Surface Defects: Check for cracks, bubbles, scratches, chips, dents, or deformities.
- Edge Smoothness: Ensure the rim and base are polished, free of sharp edges or burrs.
- Transparency/Color Consistency: Clear glass should be free of cloudiness; colored glass must have uniform hues without fading or uneven pigmentation.
1.2 Dimensions and Capacity
- Dimensional Accuracy: Use calipers to verify height, rim diameter, and base diameter against specifications (tolerance: ±2mm).
- Capacity Verification: Measure water volume poured into the jar to confirm labeled capacity (e.g., 200ml ±5%).
1.3 Material and Performance
- Glass Type: Confirm the use of heat-resistant glass (e.g., borosilicate glass) to prevent cracking under high temperatures.
- Thermal Resistance Test: Fill jars with hot water (≥90°C) or burn candles for 1–2 hours to check for cracks or deformation.
- Wall Thickness: Use a thickness gauge to ensure uniformity, especially at stress-prone areas like the rim and base.
1.4 Structural and Functional Integrity
- Stability: Place the jar upside-down on a flat surface to check for wobbling.
- Lid Fit (if applicable): Test sealing by inverting the jar with the lid closed; ensure no leaks or looseness.
- Printing/Decoration Quality: Verify that prints, labels, or engravings are smudge-free and durable (use a 3M tape test for adhesion).
1.5 Packaging and Labeling
- Inner Packaging: Inspect cushioning materials (e.g., foam, paper pads) to prevent breakage during shipping.
- Outer Carton Markings: Confirm correct product codes, quantities, manufacturing dates, and certifications (e.g., FSC, RoHS).
- Barcodes/Labels: Ensure scannability and consistency with the product.
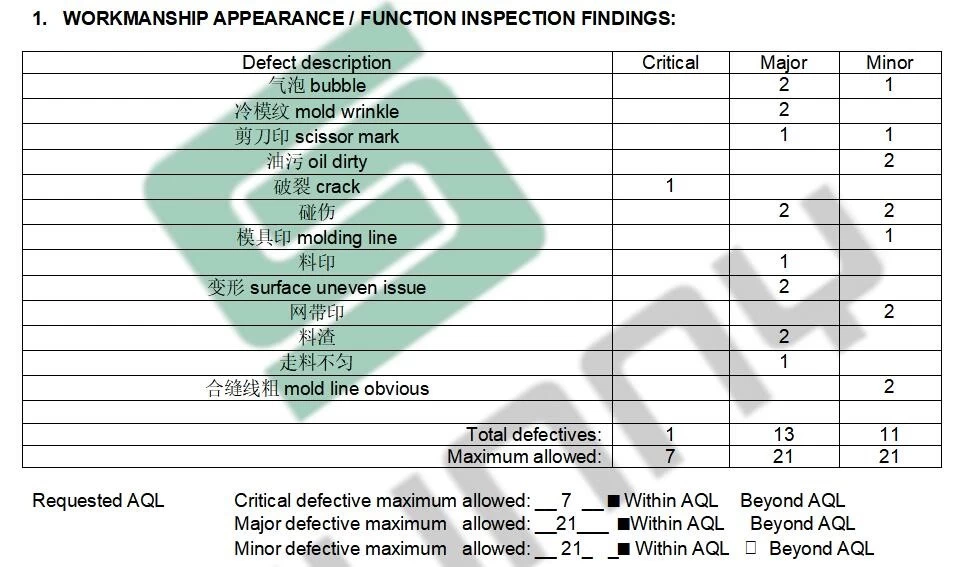
2. Inspection Process
2.1 Pre-Inspection Preparation
- Tools: Calipers, thickness gauge, measuring cup, 3M tape, color chart, flashlight, magnifying glass.
- Sampling Plan: Follow AQL Level II (e.g., ANSI/ASQ Z1.4 or ISO 2859-1). For a batch of 1,000 units, inspect 80 samples.
2.2 Step-by-Step Procedure
1. Sample Comparison: Cross-check production samples against approved prototypes or design files.
2. Initial Visual Screening: Examine all samples under natural or standardized lighting for obvious defects.
3. Dimensional Check: Measure 20% of samples for critical dimensions.
4. Functional Testing:
- Perform thermal resistance tests on 5–10 units.
- Test lid fit and decoration durability.
5. Packaging Evaluation:
- Conduct a drop test (e.g., 0.5–1m height) to simulate transport conditions.
- Verify cushioning and carton durability.
6. Documentation: Record defects (e.g., critical/minor) and calculate pass/fail rates (e.g., critical defects ≤0.4%).
3. Precautions
1. Safety Measures
- Wear gloves to avoid cuts from glass edges.
- Conduct thermal tests in a fire-safe area.
2. Environmental Conditions
- Inspect in a clean, well-lit space to avoid dust interference.
3. Standardization
- Agree with suppliers on defect criteria (e.g., maximum bubble size ≤1mm).
4. Compliance Requirements
- For export, ensure compliance with regulations like FDA (food-contact safety) or EU RoHS (hazardous substance restrictions).
5. Documentation and Communication
- Retain signed reference samples and inspection reports for dispute resolution.
4. Common Issues & Solutions
Issue 1: Excessive bubbles in glass.
Solution: Reject batches if bubbles exceed 2mm or are located in high-stress areas.
Issue 2: Faded or peeling decorations.
Solution: Require suppliers to improve curing processes or switch to UV-resistant inks.
Issue 3: High breakage rates during shipping.
Solution: Upgrade packaging with double-walled cartons or additional cushioning.
Sunny Glassware adopts extra six steps for inspection,No major quality complaints on products produced for over 10 consecutive years. By following this guide, Sunny Glassware inspectors can systematically identify defects, ensure compliance, and minimize risks of returns or safety incidents. Regular factory audits and clear communication with suppliers further enhance long-term quality control.